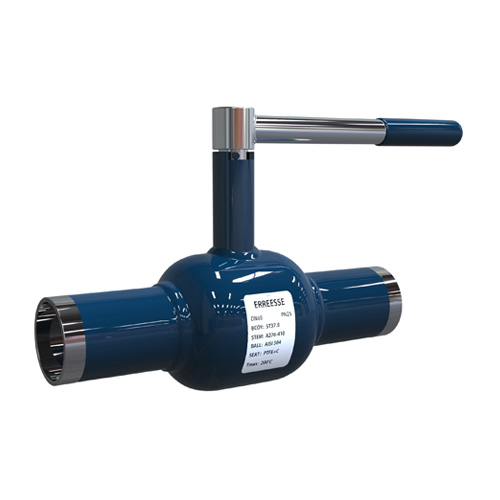
Fully welded thermal floating ball valve
Valve size: NPS1/2 ~ NPS56 DN15 ~ DN1400
Pressure rating: 150LB ~ 300LB, PN16 ~ PN40
Material: carbon steel, stainless steel
Design and manufacturing standards: ISO14313, 6D, GB/T 19672, JB/T 12006
Face to face standards: ASME B 16.10, 6D
Butt welding valve end standard: ASME B16.25, EN 12627, GB/T 12224
Flange end standard: ASME B16.5, ASME B16.47, EN 1092, GOST 12815, GB/T 9113
Stress test standards: 6D, 598, BS EN 12266 -1
Fire safety test standards: 607, 6FA, BS EN ISO 10497
Quality / Product Certification: ISO 9001, 6D, PED 2014/68/EU, EAC, ATEX and OSHAS 18001
Safety and reliability: in line with SIL3
Contact usSpecification
Valve size: NPS1/2 ~ NPS56 DN15 ~ DN1400
Pressure rating: 150LB ~ 300LB, PN16 ~ PN40
Material: carbon steel, stainless steel
Design and manufacturing standards: ISO14313, 6D, GB/T 19672, JB/T 12006
Face to face standards: ASME B 16.10, 6D
Butt welding valve end standard: ASME B16.25, EN 12627, GB/T 12224
Flange end standard: ASME B16.5, ASME B16.47, EN 1092, GOST 12815, GB/T 9113
Stress test standards: 6D, 598, BS EN 12266 -1
Fire safety test standards: 607, 6FA, BS EN ISO 10497
Quality / Product Certification: ISO 9001, 6D, PED 2014/68/EU, EAC, ATEX and OSHAS 18001
Safety and reliability: in line with SIL3
NACE: in accordance with MR 01-75 / ISO 15156
Optional valve actuators: polished rods, gears, handles, pneumatic actuators, hydraulic actuators, gas actuators,
Gas oil actuator, electric actuator, hydraulic/electric actuator, hydraulic actuator
Seal rating: 598 (zero leak), grade six (FCI 70-2), 6D
Characteristics
Fully welded body structure to avoid leakage.
Since the seat is made of a carbonized Teflon seal ring and a spring, it is highly adaptable to changes in pressure and temperature, and does not cause any leakage within the marked pressure and temperature range.
30 years of effective service life, maintenance-free, and the same life as the pipeline.
Under the action of the pressure of the floating ball valve, the ball is pushed toward the outlet end seal seat to form a tight seal.
Directly buried valves can be provided to save wells, reduce investment in previous projects, and ensure the safety of operation and maintenance personnel.
Pressure prefabricated insulation type valves can be provided to effectively avoid the lack of on-site insulation conditions.